Introduction
In the ever-evolving world of cosmetic packaging, the significance of package compatibility testing for cosmetic packaging cannot be overstated. It’s a crucial aspect that ensures the seamless interaction between the packaging material and the cosmetics it contains. This article delves into the definition of compatibility testing, its various types, real-world cases in cosmetic packaging, and the essential practices for conducting comprehensive tests.
Definition of Compatibility Testing
Compatibility testing in cosmetic packaging involves evaluating the interaction between plastic packaging and cosmetics. It encompasses three main types: chemical compatibility, physical compatibility, and biological compatibility.
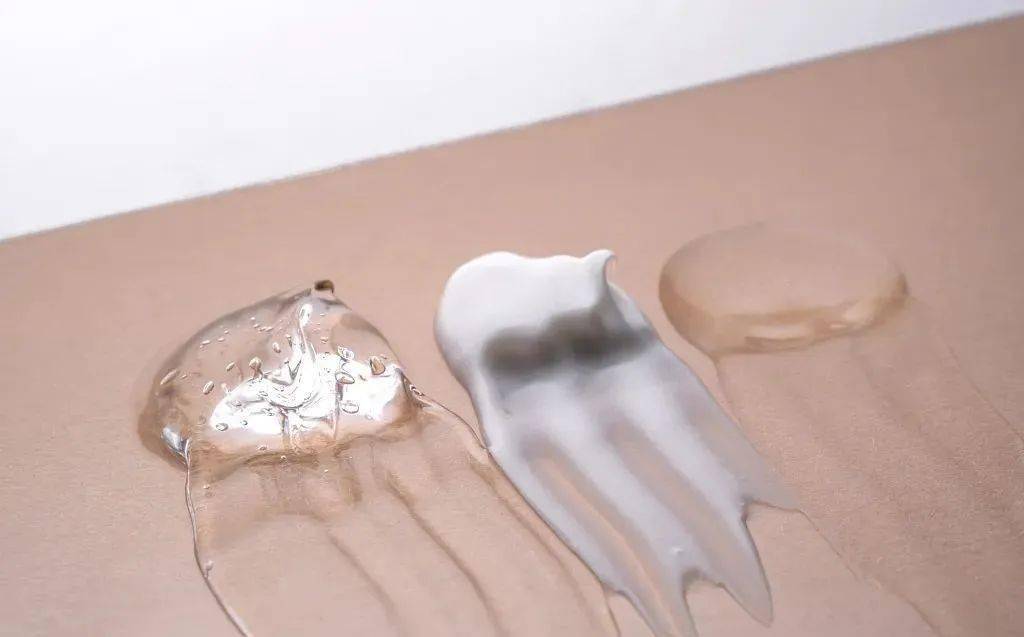
Chemical Incompatibility
Chemical incompatibility arises when the chemical components of the cosmetic packaging material react adversely with cosmetic ingredients, leading to issues such as material yellowing or changes in odor.
Biological Incompatibility
Biological incompatibility occurs when substances from the cosmetic packaging material migrate into the cosmetics, surpassing safety standards. Harmful substances like plastic additives, solvents, volatile organic compounds, and hazardous metals can pose risks.
Physical Incompatibility
Physical incompatibility involves changes in the cosmetic packaging material and its contents due to mutual influence. This can manifest as infiltration, adsorption, cracking, and dissolution.
Understanding Compatibility Test Results
Compatibility test results for cosmetic packaging are intricate, often raising questions about why certain samples exhibit issues while others do not under the same conditions. The reality is that compatibility failures exist at a certain rate, making assessing a broader sample size imperative to uncover potential problems in mass production.
Compatibility Accident Cases in Cosmetic Packaging
Case One: Sunscreen Ingredients and PET Containers
A luxury goods company faced issues when sunscreen ingredients proved physically incompatible with PET containers, leading to cracking. This incident prompted a shift to materials with more suitable properties for cosmetic packaging, emphasizing the importance of material selection.
Case Two: Color Changes in Foundation Product
A cosmetics giant experienced color changes in a foundation product due to pigmentation from the cosmetic packaging material. This case highlights the necessity of compatibility testing even when changes seem minor.
Examples of Compatibility Testing Practices for Cosmetic Packaging
To conduct thorough compatibility testing for cosmetic packaging, a cosmetic industry giant follows specific procedures tailored to the product:
- General Compatibility Testing:
- Test environments: -20°C, 4°C, 23°C, 40°C, 50°C, Light, Cyclic thermal shock, 95% humidity, 30°C
- Duration: 4-8 weeks or longer
- Stress Cracking Test:
- Test environments: 23°C, 40°C, 50°C
- Duration: 4-8 weeks or longer cycles
- Post-processing Compatibility Testing:
- Test environments: 23°C, 40°C, cyclic thermal shock, 95% humidity, 30°C
- Duration: 10 days
Evaluation at the end of the test cycle involves assessing cosmetic packaging appearance, mechanical properties, weight loss, stress rupture, aging, color migration, fragrance stability, and contents status.
Establishment of a Compatibility Laboratory for Cosmetic Packaging
Creating a compatibility laboratory for cosmetic packaging requires a strategic approach to human resources. Cross-disciplinary expertise is vital, involving professionals well-versed in cosmetic package materials and contents. Collaboration between departments ensures reliable results, preventing oversights that could compromise the integrity of compatibility testing.
In conclusion, package compatibility testing for cosmetic packaging is a meticulous process that safeguards the quality and safety of cosmetic products. Real-world cases underscore the potential consequences of overlooking compatibility issues in cosmetic packaging. By following comprehensive testing practices and establishing specialized laboratories, cosmetic companies can ensure the reliability and success of their products in the market.