The introduction of induction seals for bottles has revolutionized the packaging industry. They provide a hermetic seal that not only ensures the freshness of the product but also prevents leaks. The use of induction seals has become increasingly popular in various sectors, including beverage, dairy, and even the shipping industry. The main reason behind this is the non-contact process of induction sealing, which ensures a clean and efficient sealing process.
The induction seal consists of a foil layer and a polymer coating. When the induction sealer’s electromagnetic field interacts with the foil liner, it generates heat, causing the polymer coating to bond with the lip of the container. This results in a secure and tight seal that maintains the product’s shelf life and quality.
How Induction Sealing Works
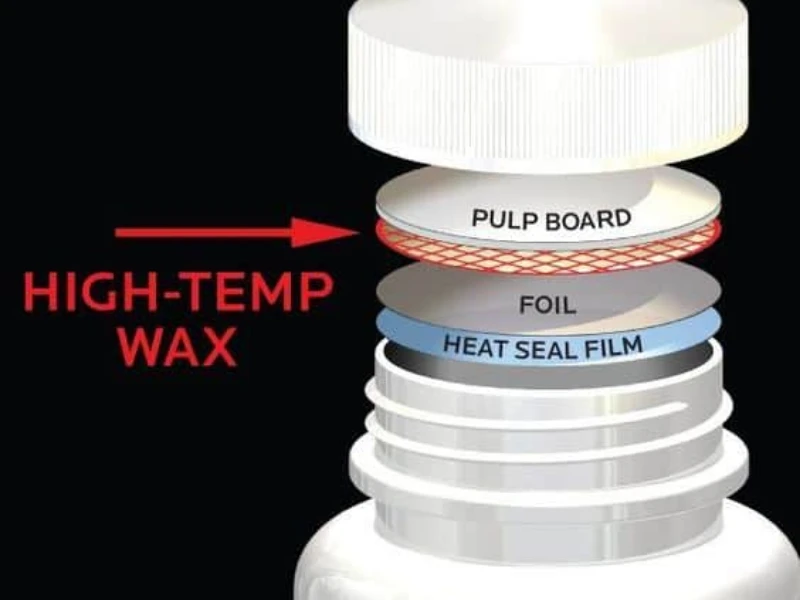
Induction sealing is a fascinating process that involves science and technology. The induction sealer, a key component of this process, generates an electromagnetic field. When the induction cap, equipped with a foil liner, passes through this field, it induces a current in the foil layer. This current generates heat, which then melts the wax and polymer coating on the foil liner, creating a bond with the lip of the container.
This process is a non-contact one, meaning the sealing head doesn’t physically touch the cap or the container. This not only ensures a clean seal but also reduces the risk of contamination, making induction sealing a preferred choice in industries like food and pharmaceuticals.
Components of an Induction Seal: Backing, Foil, and Heat Seal
An induction seal is more than just a piece of foil. It’s a complex structure made up of several layers, each playing a crucial role in the sealing process. The backing, usually made of paper or foam, provides rigidity and support. The foil layer, typically aluminum, is responsible for generating heat when exposed to the electromagnetic field of the induction sealer.
The heat seal layer, often a polymer or coating, bonds with the lip of the container when heated, creating a secure seal. Some induction seals also include a wax layer, which melts during the sealing process and is absorbed by the backing, allowing the foil and polymer to bond with the container.
These components work together to create a hermetic seal that protects the product from moisture, oxygen, and other external factors, ensuring its freshness and extending its shelf life.
The Role of Pressure, Heat, and Time in Induction Sealing
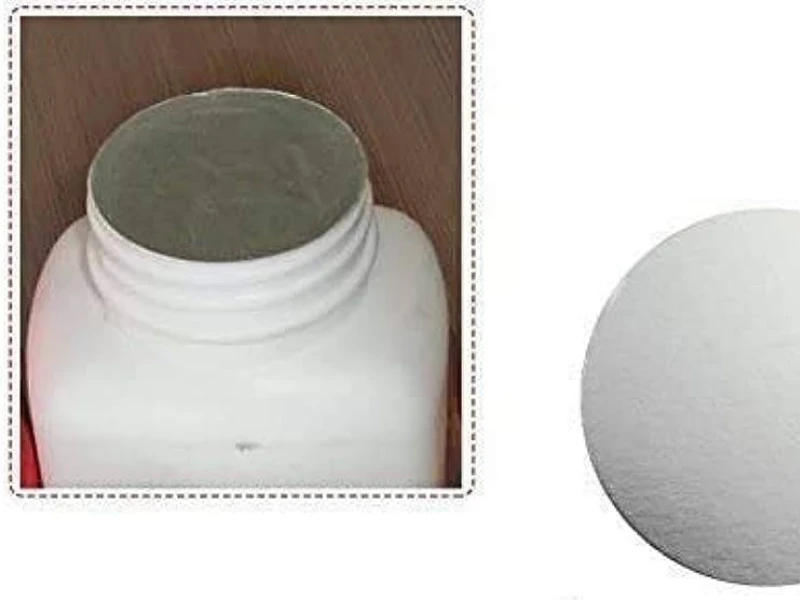
Induction sealing is a delicate process that requires the right balance of pressure, heat, and time.
The pressure applied by the induction cap ensures the foil liner is in direct contact with the lip of the container. This is crucial for a successful seal as it allows the heat to be efficiently transferred to the polymer coating.
The heat, generated by the foil layer when exposed to the electromagnetic field, is what melts the polymer coating, allowing it to bond with the container. The amount of heat generated depends on the power supply to the induction sealer and the speed of the production line. Too much heat can damage the seal or the container, while too little heat can result in an incomplete seal.
Time is also a critical factor. The sealing process needs to be long enough for the heat to melt the polymer and create a bond but short enough to prevent damage to the seal or container. The speed of the production line needs to be synchronized with the induction sealer to ensure each container is sealed properly.
Induction Sealing Process – From Power Supply to Sealing Head
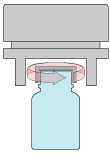
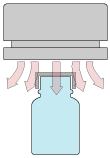
The induction sealing process starts with the power supply. The power supply generates an alternating current, which is then converted into a high-frequency electromagnetic field by the sealing head. This field induces a current in the foil layer of the induction cap, generating heat.
The heat melts the wax layer, which is absorbed by the backing, exposing the polymer coating. The heat then melts the polymer, allowing it to bond with the lip of the container. The result is a secure and tight seal that protects the product from external factors and ensures its freshness.
The sealing head plays a crucial role in this process. There are two types of sealing heads: flat heads and tunnel heads. Flat heads are used for flat caps, while tunnel heads are used for caps with a recessed area. The type of sealing head used depends on the type of cap and container.
Choosing the Right Materials – Container, Cap, and Liner
The effectiveness of induction sealing largely depends on the compatibility of the container, cap, and liner. Containers made of materials like polyethylene (PE), polypropylene (PP), and polystyrene (PS) are commonly used with induction seals. The container’s lip should be free from defects and contaminants to ensure a perfect seal.
Caps, usually made of plastic or polymer, come with an induction liner pre-inserted. The type of liner—whether it’s a one-piece or two-piece, depends on the product and its intended use. The liner’s foil layer is crucial for the induction heating process, while the polymer coating ensures the seal bonds with the container.
One-Piece vs. Two-Piece Induction Liners: What’s Best for Your Product?
Induction liners come in two main types: one-piece and two-piece. One-piece liners provide a hermetic seal and are typically used for products that require maximum protection, such as dairy or beverages. Once the seal is removed, it cannot be resealed.
Two-piece liners, on the other hand, consist of a backing and a separate foil layer. Upon sealing, the wax melts, allowing the foil and polymer to bond with the container, while the backing remains inside the cap. This type is often used for products that might be used multiple times after opening, like certain medicines or condiments.
Liner Type | Description | Typical Use |
One-Piece Liners | One-piece liners provide a hermetic seal. Once the seal is removed, it cannot be resealed. | Typically used for products that require maximum protection, such as dairy or beverages. |
Two-Piece Liners | Two-piece liners consist of a backing and a separate foil layer. Upon sealing, the wax melts, allowing the foil and polymer to bond with the container, while the backing remains inside the cap. | Often used for products that might be used multiple times after opening, like certain medicines or condiments. |
The Importance of Proper Cap Application Torque in Induction Sealing
Cap application torque is pivotal in induction sealing. Too much torque can damage the cap or container, while too little can result in a weak seal. Proper torque ensures the induction liner is in full contact with the container’s lip, allowing for efficient heat transfer and a secure seal. It’s essential to regularly check and calibrate torque settings on the production line to maintain consistent sealing quality.
Can Induction Seals Be Used on All Types of Bottles and Jars?
Induction seals are versatile and can be used on a wide range of bottles and jars made of materials like PE, PP, and PVC. However, the container’s shape, size, and material, as well as the product it holds, will determine the type of induction liner required. For instance, a dairy product might need a different liner compared to a cosmetic product.
It’s essential to consult with induction sealing experts or manufacturers to determine the best sealing solution for a specific product.
How Does Induction Sealing Compare to Other Sealing Methods in Terms of Product Quality?
Induction sealing stands out from other sealing methods due to its ability to create a hermetic seal. This seal effectively protects the product from moisture, oxygen, and other external factors, thereby preserving its freshness and extending its shelf life.
Unlike some other sealing methods, induction sealing is a non-contact process. This means the sealing head doesn’t physically touch the cap or the container, reducing the risk of contamination. This makes induction sealing a preferred choice in industries like food and pharmaceuticals, where hygiene is paramount.
Moreover, induction sealing is a reliable method to prevent leaks in bottled products. The secure seal ensures the product stays within the container, even during shipping or handling, reducing the risk of product loss and potential mess.
How Do Induction Seals Prevent Leaks in Bottled Products?
Induction seals play a crucial role in preventing leaks in bottled products. The induction sealing process creates a bond between the liner and the lip of the container, resulting in a secure and tight seal. This seal acts as a barrier, preventing the product from escaping the container.
Moreover, the seal also provides tamper-evidence. If the seal is broken or tampered with, it’s immediately noticeable. This not only reassures consumers about the product’s safety but also protects manufacturers from false claims.
Conclusion
Induction seals for bottles have profoundly impacted the cosmetic industry. In an industry where product integrity, freshness, and presentation are paramount, induction sealing offers unparalleled benefits.
By providing a hermetic seal, these seals ensure that cosmetic products, whether it’s a luxurious serum or a daily moisturizer, remain uncontaminated and retain their efficacy.
The tamper-evidence feature of induction seals also adds an extra layer of trust for consumers, assuring them of the product’s safety and authenticity. In an age where counterfeit cosmetics are a genuine concern, this assurance is invaluable. Moreover, the prevention of leaks is especially crucial for cosmetics, as leaks can compromise the product’s quality and lead to potential losses for both manufacturers and consumers.
For those in the cosmetic industry aiming to elevate their product quality and consumer trust, induction sealing is not just an option; it’s a necessity. And for those seeking expert guidance in this realm, Cosmopacks is at the forefront. With their cosmetic packaging and services, Cosmopacks can provide invaluable expertise, helping customers choose the most suitable and cost-effective sealing solutions for their projects.
By understanding and implementing this sealing method with the assistance of industry leaders like Cosmopacks, brands can ensure their products stand out in terms of quality, safety, and presentation.
Contact us today if you want to elevate your brand with innovative designs, sustainable solutions, and a commitment to functionality!